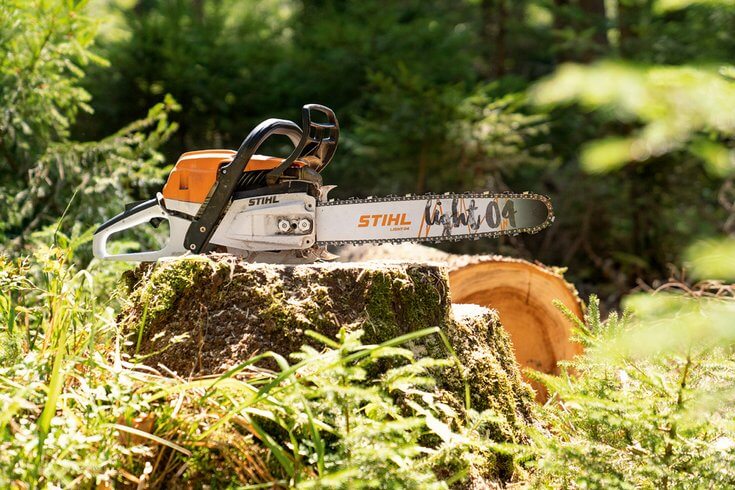
You may remember school chemistry lessons conducting experiments with magnesium to ignite it and set off a bright, white chemical reaction, but did you know that we also use magnesium parts in STIHL tools?
STIHL has over 60 years of experience working with magnesium alloys at our dedicated casting plant in Prum, Germany and it has been a core component of our machinery for many years. The most notable use of magnesium in recent years has been our development of a new lightweight piston on the MS 400 C-M chainsaw. This component gives it the highest working speed in the 60cm3 class, a formidable 14,000rpm, whilst also having an excellent weight to power ratio of 1.5 kg per kilowatt.
The state-of-the-art magnesium diecasting plant where our components are manufactured from raw magnesium through to the finished product was set up in 1971 and is currently one of the largest magnesium diecasting plants in Europe with over 700 employees. For more than 60 years, magnesium has been fabricated by STIHL for use in our machinery, as well as for other companies, such as those in the automotive industry.
STIHL recently won a top award for the magnesium piston used in the MS 400 C-M chainsaw, the world’s first chainsaw with a magnesium piston! The Award of Excellence 2020 was given by the International Magnesium Association (IMA) for the component and production process which was specifically developed for the MS 400 C-M’s piston, winning the Commercial Cast Product or Process category.
It’s not just smaller components like the piston in the MS 400 C-M that magnesium is used for though. It’s used as the crank case on the engine for many high performance professional tools, including forestry chainsaws such as the MS 261 C-M. It’s also used for pro chainsaw sprocket covers, the cutting disc guard on our TS 410 and other construction cut-off machines. And it’s used for the pole pruner heads and long-reach hedge trimmer cutter bars to help reduce weight and strain on the users, whilst remaining strong.
Magnesium has been used for years across a diverse range of products due to its mechanical properties as a material. It is lightweight, strong and stable, which is exactly what you need for power tools. It’s also optimal for casting, easy to machine and can be recycled without limit too, so at the end of a machine’s life, it can be turned back into a new machine.
The die-casting process with magnesium allows for excellent dimensional accuracy which is very important when building an engine within high tolerances, and thin walls can be used where required to reduce weight. It also has good attenuation properties to help with vibration too.
If you think back to those magnesium experiments in your chemistry lessons, you may be wondering why your STIHL chainsaw doesn’t have the same reaction?! Well, that’s because we use a magnesium alloy, known as EN-MB MgAl9Zn1(A) (AZ 91). It’s a catchy name, we know! But this is actually the most common diecasting alloy due to its casting properties and mechanical strength. It is used in everything from automotive parts to sports equipment and household appliances.
You can find out more about our magnesium diecasting plant and even watch a virtual factory visit at www.magnesium.stihl.com/.
Can you please tell me who makes the STIHL branded cylinders for the new generation saws? I own an MS462 made in november 2018 and I would like to know this detail. Some guys say it’s MAHLE behind these cylinders, is it true?
Hi Lilian, thanks for your comment. We cast a lot of our own magnesium components ourselves but I’m afraid we can’t share specific information about the suppliers of all of our components. Thanks, STIHL GB
I love my 025 chainsaw. Flawless for 20 years. Coil went out this year replaced with aftermarket. It lasted approximately 2 hours. Got another stihl coil on the way. Hopefully it lasts long as original. Thank you stihl.
Thanks for your great feedback – fingers crossed the chainsaw lasts another 20 years! Thanks, STIHL GB
Why did Stihl change the model numbers from (example 026) to MS 260
Hi, thanks for your comment. The 0 was removed across all STIHL product to help make the naming system more simple and consistent and give us more numbers to work with! The first number now gives an indication of where each product sits in the range (i.e. an MS 462 C-M being more powerful than an MS 261 C-M). Thanks, STIHL GB
Just ordered an MS 462 R here in the USA., for use in Wisconsin USA. Looks like a dynamite saw..
I’m replacing an old 017 saw of 27 years.. that still runs fantastic!!..
MY QUESTION IS
what basic components have been enhanced to give that saw a higher acceleration rate, and what amount of increase in RPM resulted during testing?
Also, do you require and run endurance testing for to provide a better MTBF under a load ?
YES I’m an Engineer, NOW retired from the AVIONICS and medical industry.
Sthil saws are the Standard here in the MIDWEST!!
THANKYOU!!
Konrad Bents
Hi, thanks for your comment. The MS 462 C-M has faster acceleration for a number of reasons including M-Tronic electronic ignition for early ignition and enrichment and a lightweight flywheel with a smaller diameter. This also means there is less gyroscopic force for the user. There isn’t an increase in operating rpm though, it’s still in line with MS 441, MS 461, MS 440 at 13500 rpm. The MS 462 C-M also has an optimised combustion chamber and intake diameters which help give it a wide torque and power curve. The lighter Mg piston in the MS 400 C-M allows 14,000 rpm though. When launching new models, we run extensive bench testing as well as real end user testing in key markets. Thanks, STIHL GB
Fixing up an old 2006 460
How does one try and find replacement Piston/Crankshaft/Piston housing that are as quality as the OEM parts of the same specific kind?
I don’t want to purchase parts that wont last. What would you do
Hi, thanks for your comment. Could you drop an email to our Customer Services team? They will be able to help advise whether any of our current STIHL spare parts will still fit your 460. If you can provide them with the serial number of the machine too, that will help them too. You can contact them via email to enquiries@stihl.co.uk or call them on 01276 20202. Thanks, STIHL GB
How many hours of bench testing were performed on the magnesium piston to assure its durability and resistance to heat?
Is there a coating on the magnesium alloy piston and if that coating wears off will that result in catastrophic failure?
What is the combustion temperature for magnesium piston and what temperatures do the chainsaw cylinders reach when firing?
Now that the MS 400 cm has been released several years, what issues of the model have been submitted for warranty review?
Hi, thanks for all the questions. To develop a magnesium piston in a chainsaw took many years of testing and called upon all our years of manufacturing magnesium products until we were satisfied the piston could meet the same working hours of that in the MS 362 C-M. Unfortunately, due to the significant time and investment which went into this “world’s first”, we are not able to openly share this information in a public domain. Thanks, STIHL GB